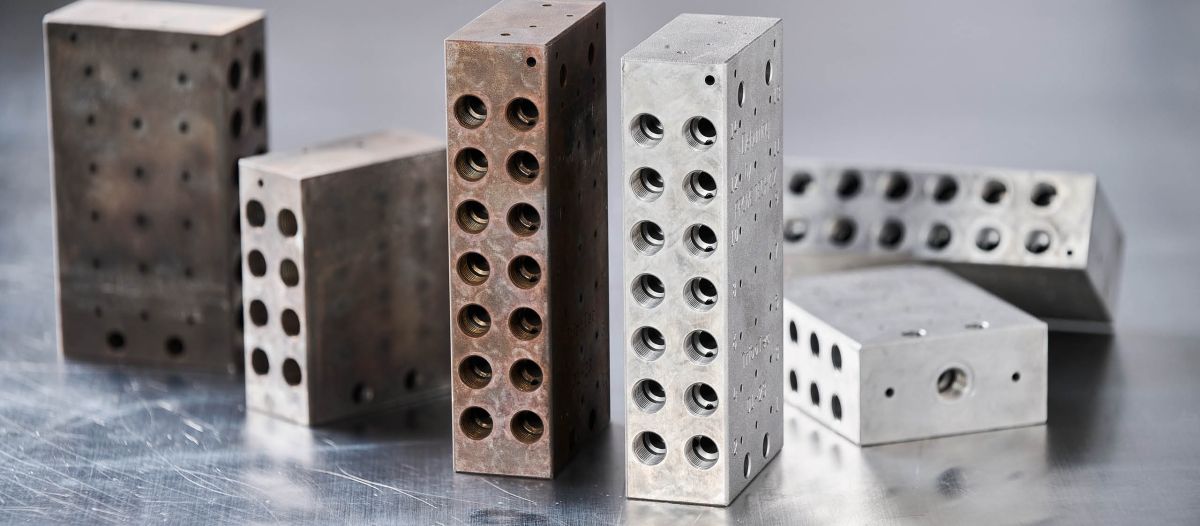
After parts are deburred, they require cleaning, and this is where
DST-CHEMICALS plays a vital role. Discover how to clean these parts using our customized products, which are specially tailored to meet your needs. Additionally, learn why it is important to clean parts after deburring. But first, let us start at the beginning of the process and explain what deburring is.
Table of Contents
What is deburring?
Deburring is the process of removing burrs, which are unwanted rough edges or protrusions on a material, usually formed during manufacturing operations like cutting, drilling, or milling. Deburring plays a crucial role in improving part quality by ensuring smooth surfaces, proper fit, and better performance. It helps in enhancing the functionality, aesthetics, and safety of the finished product. In summary, deburring is necessary to maintain quality, enhance product performance, and improve overall functionality.
Significance of deburring in manufacturing
Deburring plays a crucial role in several aspects of the manufacturing process. First, deburring improves the functionality and performance of components, ensuring they fit seamlessly together and operate smoothly. Furthermore, it enhances the overall quality and aesthetics of the finished product. Smooth, burr-free surfaces not only look more professional but also minimize the risk of injury during handling or assembly.
By eliminating burrs, manufacturers can enhance the lifespan and reliability of their products, ultimately increasing customer satisfaction and loyalty.
Read more about our metal cleaning products in manufacturing here
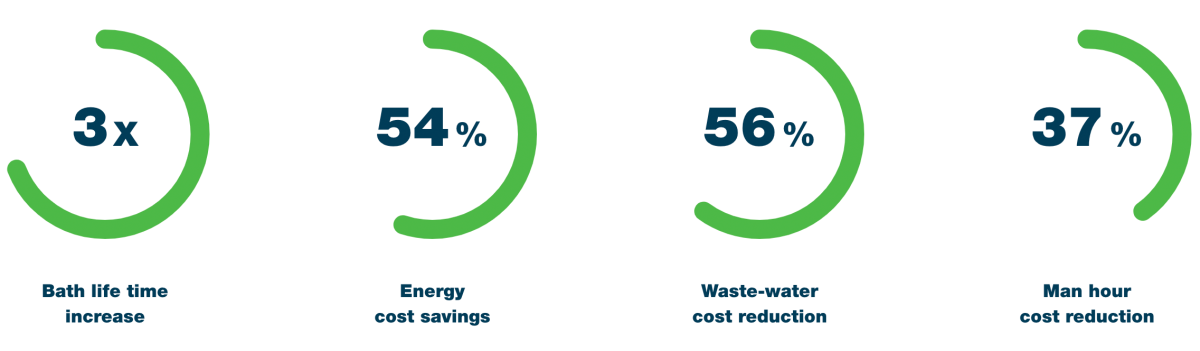
We’re experts in cleaning after the deburring process
When it comes to cleaning solutions after a deburring process, we, at DST-CHEMICALS, stand out as a leader in the industry. With 35 years of experience and expertise, we offer cleaning solutions of high quality and functionality aimed at washing the parts after a deburring process that are covered with oxides, ultimately, removing them in the process.
The deburring process
At DST-CHEMICALS, we mainly have cleaning products for a cleaning process after TEM and ECM. However, there exists methods and techniques used to remove burrs, depending on factors such as the material being worked on, the size and types of burrs, production volume, and desired level of precision. Here are some common deburring methods:
Manual deburring
This method involves using handheld tools like flies, abrasive stone, or sandpaper to manually remove burrs. It is suitable for small-scale or intricate workpieces, but it can be time-consuming and labor intensive.
Pros
- Cost-effective for small-scale production or one-off projects.
- Provides precise control over the deburring process.
- Suitable for delicate materials or intricate parts.
Cons
- Time consuming, especially for large-scale production.
- Requires skilled labor, leading to higher labor costs.
- May result in inconsistent deburring if not performed meticulously.
Mechanical deburring
This method uses machines to remove burrs. These machines can be equipped with rotating brushes, abrasive belts or abrasive wheels. They provide consistent and efficient deburring for larger workpieces or high-volume production.
Pros
- Faster and more efficient than manual deburring.
- Consistent deburring results for large quantities of parts.
- Reduces labor costs compared to manual deburring.
Cons
- Initial investment in machinery can be costly.
- Limited to parts that can fit within the capabilities of the equipment.
- Potential for over-deburring if not carefully controlled.
Thermal deburring (TEM)
The TEM deburring process uses the ignition of a combustible gas within a pressurized chamber to remove burrs from machined components. Because the burrs are much smaller than the component, they reach the auto-ignition point instantly and are vaporized in the oxygen-rich chamber. An oxide layer is left across the component surfaces and in most cases, this needs to be cleaned prior to the next step, or as part of subsequent coating process. An accurately defined mixture of gases is fed into the deburring chamber via a gas metering system and ignited by a spark. The temperature of the subsequent combustion ranges from 2.500 to 3.300 °C and raises above the ignition temperature of the burr.
Read more about neutral cleaning after TEM
Pros
- Effective in removing burrs from complex and hard-to-reach areas.
- Can be used on various types of metals and alloys.
- High deburring precision.
- Short cycle times.
Cons
- Safety concerns due to the potential risks associated with working with combustible gases.
- High equipment and operational costs.
- Possibility of surface discoloration or distortion.
Electrochemical deburring (ECM)
ECM is deployed to remove unwanted burrs from metal workpieces. It uses electrochemical reactions to dissolve the burrs without causing damage to the surrounding material. Here are the pros and cons of ECM.
Read more about neutral cleaning after ECM
Pros
- Precise and controlled removal of burrs without altering the workpiece surface.
- Can target specific areas requiring deburring.
- Faster deburring process compared to manual methods.
- Lower risk of surface damage or distortion.
Cons
- Limited effectiveness on large burrs or burrs in hard-to-reach spots.
- Limited applicability to certain metals and alloys.
- Higher initial investment in equipment and setup
- Dependency on the electrolyte solution and its maintenance.
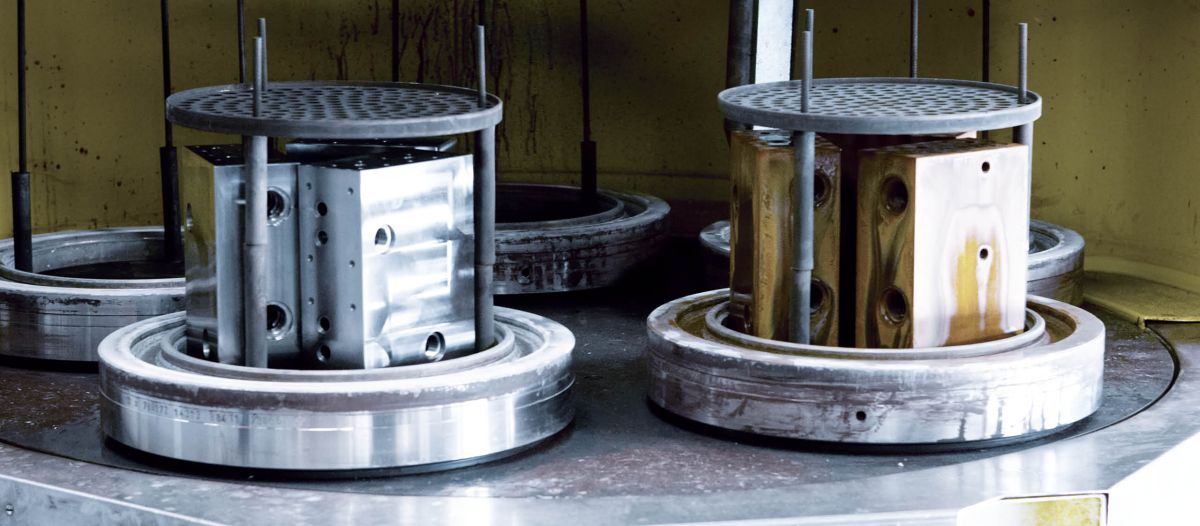
Deburring parts to perfection
Deburring is the process of removing sharp edges or burrs from a workpiece. It is a crucial step in manufacturing, as these burrs can pose safety risks, hinder the functionality of the parts, or cause damage during assembly or use. The need for deburring arises in various materials, including metal, aluminum, copper pipes, and plastic parts.
Metal parts are commonly subject to deburring due to the nature of their manufacturing processes such as machining, casting, or stamping. Burrs and sharp edges can be present on materials like steel, stainless steel, aluminum, brass, and copper. Deburring with methods like grinding, filing, or abrasive blasting can remove the sharp edges and produce smooth surfaces.
Aluminum parts can be challenging to deburr due to their tendency to clog deburring tools and the potential for smearing the material if not approached correctly. Common deburring methods include abrasive blasting, sanding, or using deburring brushes to achieve clean and smooth edges.
How we can help you in the deburring process
DST-CHEMICALS is a renowned and trusted partner in the field of cleaning solutions after deburring, offering innovative solutions and expertise that set them apart from others in the industry. We follow a unique approach to cleaning after a deburring process known as the Pure Performance Concept, which ensures the highest level of quality and efficiency in cleaning after a deburring process. Here’s why we are the go-to partner for cleaning solutions after deburring:
Expertise and experience: We boast a team of experts with extensive knowledge of cleaning after deburring different types of parts and materials. Our understanding of various deburring techniques, and chemical formulation enable us to provide customized solutions for even the most complex cleaning challenges.
Our Pure Performance concept is based on our commitment to delivering the highest level of performance in every aspect of the deburring process. Depending on what deburring method you choose, we have chemical cleaning formulations to meticulous process optimization and precise quality control, we make sure that every part is cleaned to perfection.
We understand that every customer has unique requirements and challenges. We provide comprehensive support, collaborating closely with our clients to analyze their needs, conduct trials, and develop optimized deburring processes. Our customer-centric approach ensures that the final clean after deburr operation meets and exceeds expectations.
See how we have helped others
We’ve done it before. Actually, we have helped professionals like you bring new life to machines since 1987. Roland Fleischer GmbH is a prime example of this.
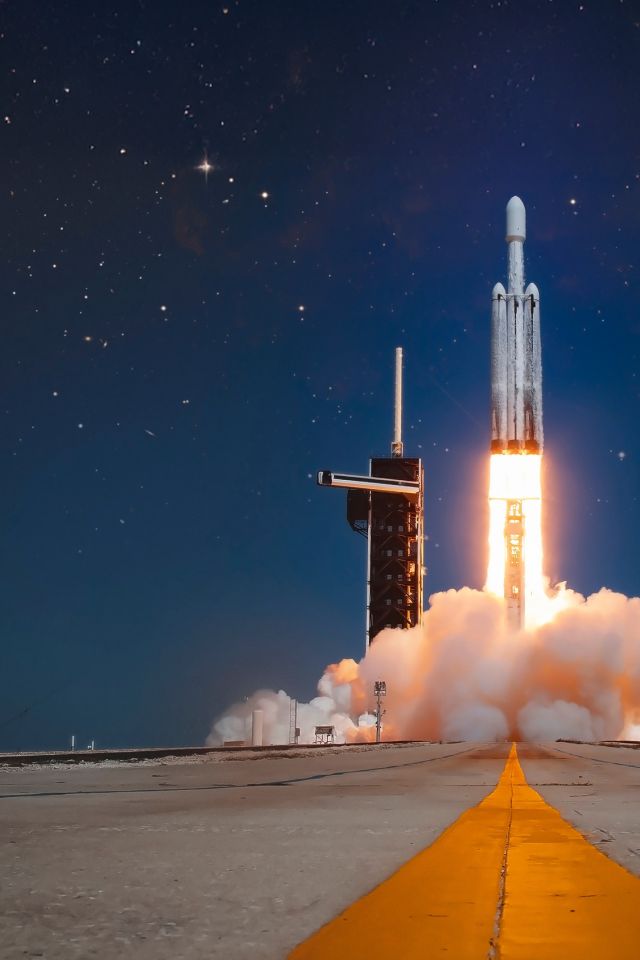
Roland Fleischer
Optimising contract deburring
Roland Fleischer GmbH is a German company specialising in CNC machining and contract deburring for hydraulic blocks and plates. They provide high-quality, efficient deburring services, reducing the need for manual rework and improving the quality of finished products.
Why you should clean after deburring
It is very important to clean a piece after a deburring process, particularly in thermal and electrochemical deburring, due to the following reason:
The deburring process generates burrs, scales, chips, oxides, and other loose particles that can remain attached to the workpiece. Cleaning helps to remove these debris, preventing them from interfering with subsequent processes or causing damage to the equipment or machinery.
TEM and ECM deburring processes can introduce contaminants or residues onto the workpiece surface. Cleaning ensures the removal of any residual chemicals, oxides, or other substances that may have accumulated during the deburring process. This promotes a clean and smooth surface finish, meeting the desired specifications and enhancing the overall aesthetics of the products.
Prevention of corrosion: If the workpiece is not thoroughly cleaned after ECM deburring, any residual chemicals or electrolytes used in the deburring process can stay on the surface. This can lead to corrosion over time. Cleaning helps to eliminate these corrosive substances, protecting the workpiece from potential damage.
Failure to clean a workpiece after deburring can result in the contamination of subsequent processes or assemblies. Loose burrs, debris, or residues left on the surface may inadvertently mix with lubricant, coating, or other materials used in further manufacturing stages. This can compromise the performance, functionality, or durability of the final product, leading to potential product failures or customer dissatisfaction.
Cleaning the workpiece after deburring is crucial for accurate quality control and process validation. By thoroughly cleaning the surface, any remaining burrs or defects can be clearly identified and assessed. This allows for proper evaluation of the deburring process, ensuring its effectiveness and reliability, and enabling necessary adjustments or improvements to be made.
Overall, cleaning a piece after deburring, especially in thermal and electrochemical deburring, maintains the integrity, quality, and performance of the workpiece, minimizing potential issues and ensuring the success of subsequent manufacturing processes.
Questions and answers
What is the purpose of deburring?
Deburring is done to remove burrs and sharp edges from the surface of a workpiece, improving its safety, functionality, and overall aesthetics.
What are the methods of deburring?
There are several methods of deburring, including manual deburring, mechanical deburring, thermal deburring, and chemical deburring. The choice of method depends on factors such as material type, part complexity, desired finish, and production volume.
What tool is used to deburr?
Various tools are used for deburring, such as deburring blades, brushes, grinding wheels, or abrasive belts. The selection of the tool depends on the material type and the size and shape of the burrs to be removed.
What does it mean to deburr material?
Deburring refers to the process of removing burrs, which are unwanted metal or material projections, and smoothing the surface of a workpiece to eliminate sharp edges, improve functionality, and enhance safety.
Why is deburring done?
Deburring is done for several reasons. It improves the overall quality and appearance of the workpiece, reduces the risk of injury due to sharp edges, and ensures proper fit and functionality when assembling parts. Moreover, deburring helps to prevent damage to equipment and extends the lifespan of the finished product.
Nick Bjerregaard
International Process & Technical Manager
Technical Manager at DST-CHEMICALS: 20 years of chemical industry experience, driving innovation, efficiency, and environmental sustainability.
Environmental, social, and governance
At DST-CHEMICALS, sustainability is at the heart of everything we do. We engaged with key stakeholders, including our team of suppliers, to ensure we focused on what truly mattered. Ready to see the full picture? Keep an eye out for our ESG report, where we share the next steps in our journey to sustainability.