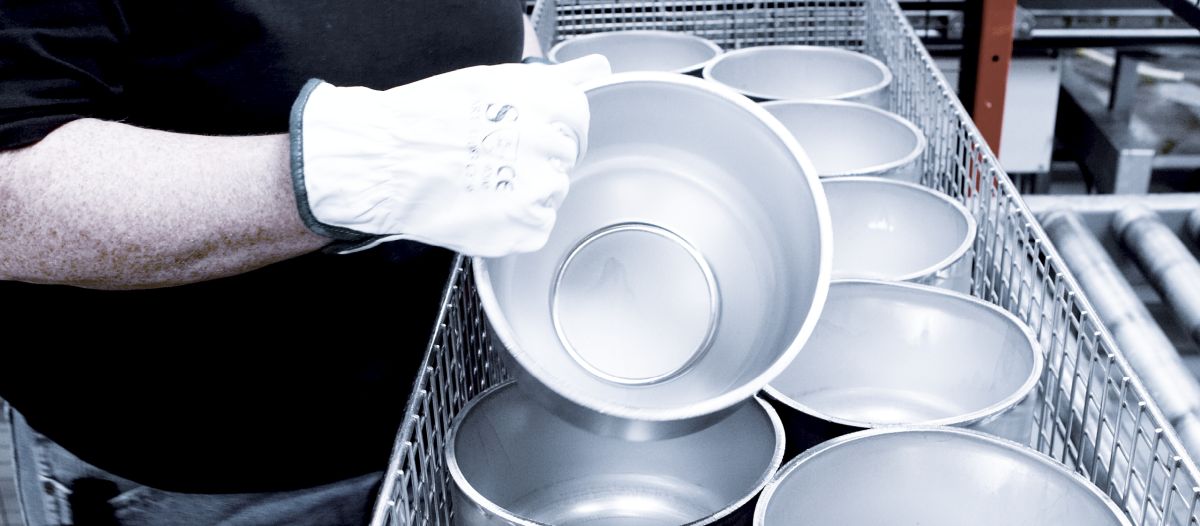
Corrosion is a major concern in industrial settings, as it can result in significant damage to equipment and structures, leading to costly repairs and downtime. In this blog, we will explore the various types of corrosion that can occur in industrial environments and discuss the most effective methods for protecting against corrosion. We will also provide practical tips and explain how we can help you tackle the challenge of corrosion protection from your parts and production.
Table of Contents
What is corrosion?
Corrosion is the deterioration of a material, usually a metal, due to a chemical reaction with its environment. There are several types of corrosion, including uniform corrosion, localized corrosion (such as pitting corrosion and crevice corrosion), galvanic corrosion, and stress corrosion cracking. Each type of corrosion can have different mechanisms and causes, but all can lead to significant damage if left unchecked.
Corrosion can have far-reaching consequences on infrastructure and industrial equipment. It can weaken structures, pipelines, and machinery, leading to premature failure and safety hazards. Corrosion can also result in leaks, reduced efficiency, and increased maintenance costs. In extreme cases, corrosion-related failures can cause catastrophic accidents and environmental damage.
The financial impact of corrosion on infrastructure and industrial equipment can be substantial. Repairing or replacing corroded components can be costly, not only in terms of material and labor expenses but also in terms of lost production and downtime. Corrosion-related maintenance and repair costs can quickly add up, affecting the bottom line of businesses and industries.
In addition to financial losses, corrosion poses a significant risk to operational safety and efficiency. Corroded equipment and structures may not perform as intended, increasing the likelihood of accidents and distributions to operations. Corrosion can also compromise the integrity of critical systems, putting personnel and the environment at risk. Ensuring proper corrosion protection measures are in place is essential for maintaining operational safety and efficiency in industrial settings.
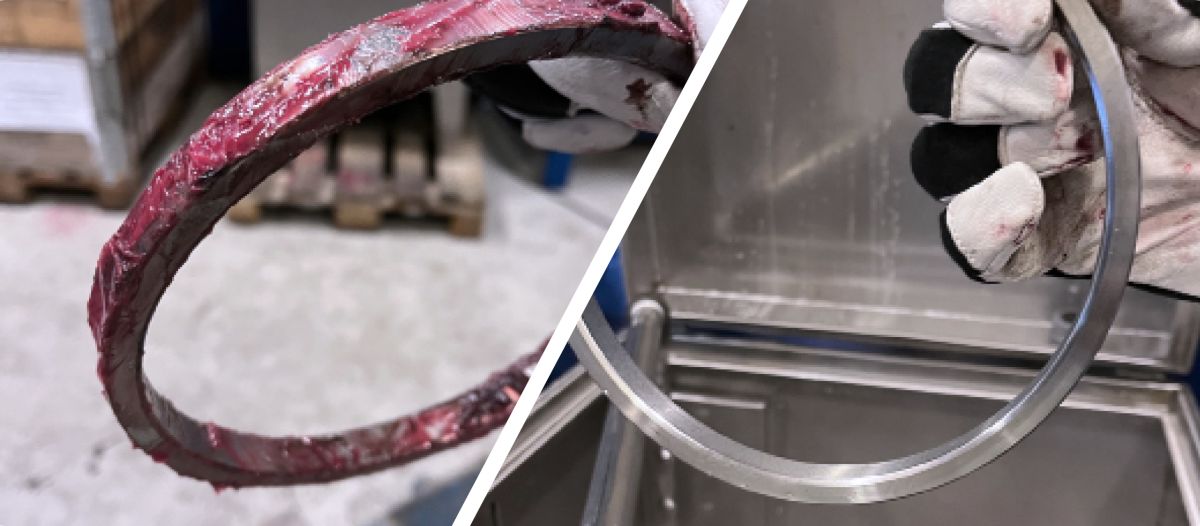
Why is corrosion protection important?
Preventing corrosion through effective protection measures can result in significant economic benefits. By safeguarding infrastructure and industrial equipment from corrosion, businesses can avoid costly repair and replacement expenses. Regular maintenance and applying corrosion protection coatings can extend the lifespan of assets, reducing the need for frequent replacements and downtime. Additionally, implementing corrosion protection measures can improve operational efficiency and reduce maintenance costs in the long run.
Corrosion not only affects the bottom line of businesses but also has environmental implications. Corrosion-related leaks and failures can result in the release of hazardous materials into the ecosystems, contaminating soil and water sources. This can have far-reaching consequences on wildlife, vegetation, and human health. Implementing corrosion protection measures helps prevent environmental damage by reducing the risk of leaks and spills.
How to prevent corrosion
The key to preventing corrosion is to eliminate or control the factors that contribute to the degradation of materials. This can be achieved by implementing various corrosion prevention techniques, including the use of barriers and inhibitors.
Barriers are physical coating or layers applied to the source of a material to prevent contact with corrosive elements. They act as a shield, protecting the underlying material from the environment. Inhibitors, on the other hand, are chemical substances that are added to the environment or applied directly to the material to reduce the rate of corrosion. Inhibitors work by forming a protective film on the metal surface, slowing down the corrosion process.
Common corrosion protection techniques
Surface Coatings: Applying paints, enamels, or other coating materials to the surface of a material can provide an effective barrier against corrosion. These coatings create a protective layer that shields the material from exposure to moisture and chemicals, preventing corrosion.
Cathodic Protection: Is a technique used to control corrosion by making the metal surface the cathode of an electrochemical cell. This can be achieved through sacrificial anodes, where a more reactive metal is connected to the structure to absorb the corrosion, or through impressed currents, where an external power source is used to provide a protective current.
Alloying metal: Alloying is the process of adding other elements to a metal to enhance its corrosion resistance. By altering the composition of the metal, its susceptibility to corrosion can be reduced, making it more resistant to degradation in corrosive environments.
Protective Wraps and Tapes: Wrapping materials like tapes and wraps can be used to physically shield metal surfaces from corrosive elements. These protective wraps create a barrier that prevents direct contact between the metal and the environment, reducing the risk of corrosion.
Corrosion Inhibitors: Corrosion inhibitors are chemicals added to the environment or applied directly to the metal surface to reduce corrosion rate. These inhibitors work by forming a protective layer on the metal surface, preventing corrosive agents from reaching the underlying material. Corrosion inhibitors are commonly used in various industries, such as oil and gas, water treatment, and manufacturing, to protect equipment and infrastructure from corrosion.
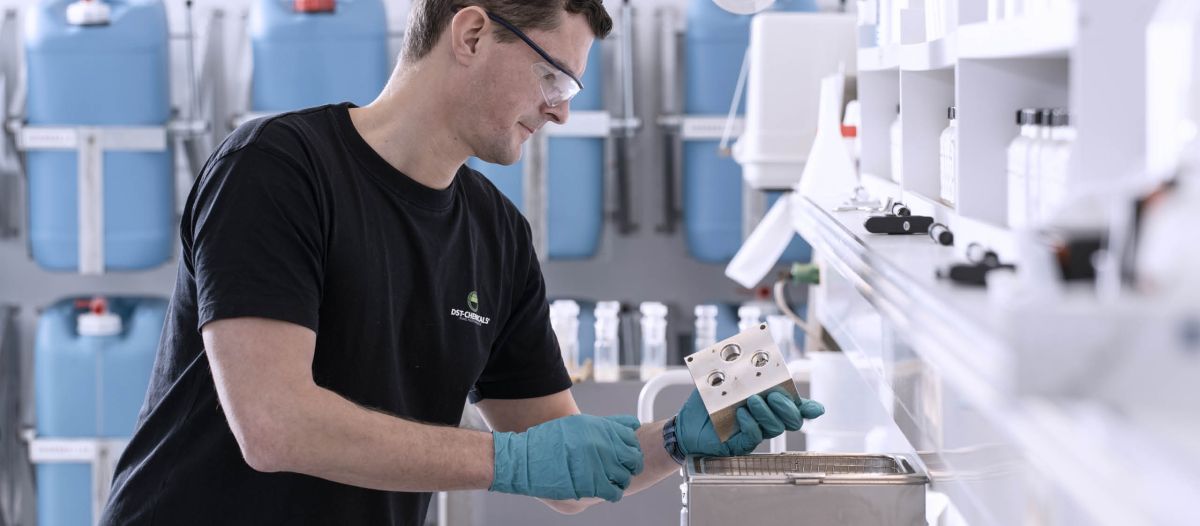
When is corrosion protection applied?
The transportation industry, particularly in overseas operations, is highly vulnerable to corrosion due to exposure to harsh environmental conditions such as humidity, saltwater, and varying temperatures. These factors accelerate the corrosion process, leading to structural degradation and potential safety hazards. Additionally, the constant movement of goods and vehicles increases the likelihood of physical damage, which can further exacerbate corrosion issues. Proper corrosion protection measures are essential to ensure the longevity and safety of transportation assets in such challenging environments.
The offshore industry: Maritime structures, including ships, offshore platforms, and port facilities, are constantly exposed to corrosive saltwater environments. The corrosive nature of seawater can accelerate the degradation of metal surfaces, making corrosion protection essential in the maritime industry.
Oil and gas pipelines are highly susceptible to corrosion due to the harsh operating conditions they are exposed to, such as high temperatures, pressures, and corrosive chemicals. Corrosion in pipelines can lead to leaks, spillages, and environmental contamination, making effective corrosion protection crucial in this industry.
Corrosion protection of metal parts is essential to prevent damage and extend the lifespan of equipment. At DST-CHEMICALS, we offer a unique solution for this challenge. We call it DST-PAS. This product is a high-performance corrosion inhibitor that forms a protective layer on metal surfaces, preventing oxidation and corrosion. This innovative product is designed to effectively protect metal parts from harsh environmental conditions, such as moisture, saltwater, and chemicals.
Factors influencing the decision to apply protection
The prevailing environmental conditions, such as temperature, humidity, moisture levels, and exposure to corrosive agents, play a significant role in determining the type and frequency of corrosion protection measures needed.
The operating conditions of assets, including stress, pressure, and operating temperatures, can impact the rate of corrosion and influence the decision to apply protection measures.
Budget constraints and cost-effectiveness are important factors to consider when deciding on the timing and extent of corrosion protection measures. Balancing the cost of protection with the potential economic losses from corrosion damage is crucial in decision-making.
Compliance with industry regulations and standards related to corrosion prevention can also influence the timing and extent of protection measures. Industries must adhere to regulatory guidelines to ensure the safety and integrity of their assets.
How can we help you in corrosion protection?
With over 35 years of expertise, we have successfully assisted numerous companies in overcoming the challenges of corrosion protection with our DST-PAS as mentioned earlier. Our customers are captivated by its exceptional functionality for both long- and short-term protection. Whether transporting goods overseas, the DST-PAS effectively shields against humidity and complies with all finishing passivation standards, even functioning optimally at 20°C. Furthermore, our water-based DST-PAS products boast a pH range from neutral to slightly alkaline, meticulously formulated to cater to all metal types while prioritizing a safe working environment. Imagine the convenience of painting directly on parts without the need for additional washing – a reality achievable with DST-PAS. Simplifying indoor storage with its temporary corrosion inhibitor, DST-PAS truly enhances efficiency and ease in your operations.
The key benefits of using DST-PAS for corrosion protection include:
It helps prevent corrosion damage, allowing metal parts to last longer and remain in optimal condition.
By reducing the frequent repairs and replacements due to corrosion, our DST-PAS can help save on maintenance costs.
Corrosion-free metal parts maintain their structural integrity and functionality, ensuring optimal performance of equipment.
The DST-PAS is formulated with eco-conscious ingredients, making it safe for use in various industries without harming the environment.
Questions & Answers
What Is the Best Way to Prevent Corrosion?
The best way to prevent corrosion is using protective coatings, cathodic protection systems, corrosion inhibitors, and regular maintenance and inspections of assets.
Which Materials Are Most Susceptible to Corrosion?
Materials such as steel, iron, aluminum, copper, and alloys containing these metals are most susceptible to corrosion due to their reactive nature and exposure to environmental factors.
How Often Should Corrosion Protection Measures Be Checked?
It depends on time, distance, and products. The metal part may only require protection during the duration of moving the component from point A to point B, which could range from a few hours to days, weeks, or even months. Therefore, it is not accurate to state that a minimum annual check is necessary; the inspection frequency depends on the level of corrosion protection needed.
Which of the Following Is Not a Method of Corrosion Protection?
Chemical cleaning is not a method of corrosion protection. Chemical cleaning involves removing contaminants and debris from surfaces but does not provide long-term protection against corrosion.
Nick Bjerregaard
International Process & Technical Manager
Technical Manager at DST-CHEMICALS: 20 years of chemical industry experience, driving innovation, efficiency, and environmental sustainability.
Environmental, social and governance
At DST-CHEMICALS, sustainability is at the heart of everything we do. We engaged with key stakeholders, including our team of suppliers, to ensure we focused on what truly mattered. Ready to see the full picture? Keep an eye out for our ESG report, where we share the next steps in our journey to sustainability.