Industrial degreasing is a crucial process in the manufacturing and maintenance industry that is often overlooked. When equipment, machinery, parts and surface are not properly degreased, they can suffer from reduced efficiency, decreased longevity, and costly breakdowns. In this blog post, we will demystify industrial degreasing by exploring its importance in enhancing efficiency and equipment longevity.
Table of Contents
What is industrial degreasing?
Industrial degreasing is the process of removing contaminants such as oils, greases, lubricants, dust, dirt, and residues from equipment and parts. These contaminants can build up over time and cause a variety of issues, including increased friction, overheating, corrosion, and mechanical failures. By removing these contaminants through degreasing, performance can be improved, leading to increased efficiency and longevity.
Understanding degreasers
Degreasers are typically composed of surfactants that work together to break down and dissolve substances. Surfactants are responsible for reducing surface tension, allowing the degreaser to penetrate and lift contaminants off surfaces.
There are various types of degreasers available on the market, each formulated for specific applications and surfaces. Some degreasers are water-based, while others are solvent-based. In addition to cleaning surfaces, degreasers also play a crucial role in preparing surfaces for coatings or treatments.
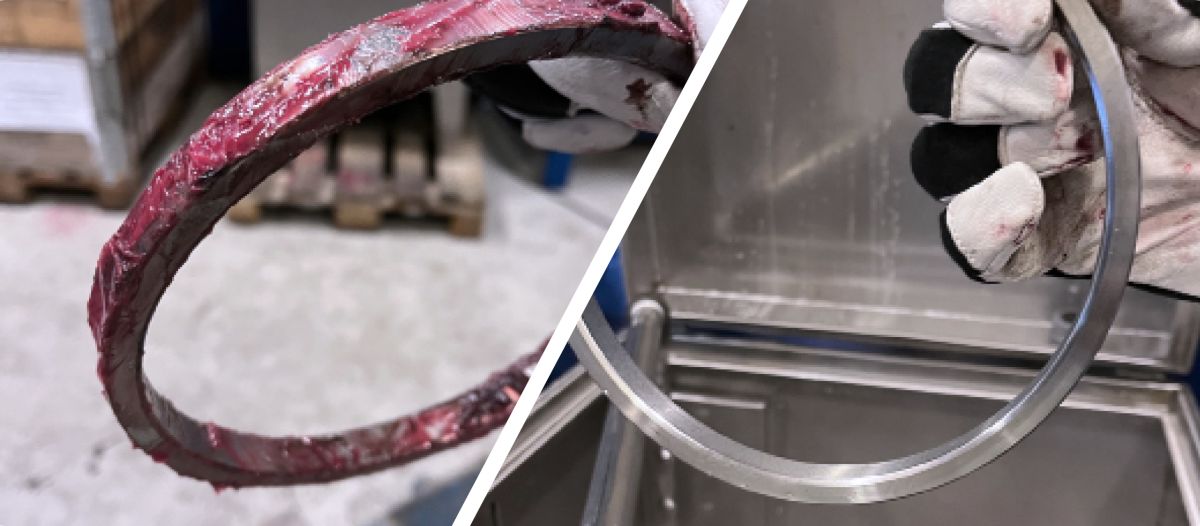
Importance of degreasing for parts
When it comes to industrial degreasing, there are various methods that can be employed to effectively remove contaminants from surfaces and parts. Two common methods are solvent-based degreasing and water-based degreasing, each offering unique benefits and considerations.
Water-based degreasing relies on the power of water and surfactants to remove contaminants from the surfaces. Water-based degreasers are eco-conscious, non-toxic, and safer for workers to use. They are suitable for cleaning water-soluble contaminants and are generally less harsh on surfaces compared to solvent-based degreasers.
On the other hand, solvent-based degreasers involve using chemical solvents to break down and dissolve contaminants. While solvent-based degreasers can be effective, they can be harsh on the environment and pose health risks to workers if not used properly. It is essential to follow safety guidelines and proper disposal procedures when using solvent-based degreasers.
It is important to note that the effectiveness of a cleaner on heavy oils can depend on various factors, including the specific formulation of the cleaner and the nature of the oil.
Tips for selecting the appropriate degreasing method include:
Identify the type of contaminants: Determine whether the contaminants are oil-based or water-soluble to choose between solvent-based and water-based degreasers.
Consider surface materials: Some surfaces may be sensitive to certain chemicals, so it is essential to select a degreasing method that will not cause damage.
Environmental impact: Consider the environmental impact of the degreasing method and choose an eco-conscious option if possible.
Safety precautions: Ensure that proper safety measures are in place when using degreasers, especially solvent-based solutions, to protect workers and the environment.
Degreasing plays a crucial role in maintaining the efficiency and performance of parts and equipment in various industrial settings.
-
Reduced Friction: One of the primary benefits of degreasing is the reduction of friction between moving parts. Oils and greases can create a layer of residue that increases friction, leading to wear and tear on components. By removing these contaminants, degreasing helps to reduce friction and prolong the lifespan of parts. -
Improved heat dissipation: Oily residues can act as insulators, trapping heat and inhibiting the proper dissipation of heat generated by parts. Degreasing helps to remove theme insulating layers, allowing for better heat dissipation, and preventing overheating, which can lead to equipment failure. -
Enhanced performance: Clean parts operate more efficiently, leading to improved performance and productivity. Degreasing ensures that components can function optimally without hindrance of contaminants, resulting in smoother operation and reduced downtime. -
Safety implications: Proper degreasing also has important safety implications in the workplace. Oily residues left on parts can create slippery surfaces that increase the risk of slip and fall accidents caused by oily residues is significantly reduced, creating a safer work environment for employees. -
Prevention of Accidents: Accidents can occur when parts malfunction due to the buildup of contaminants like oils and greases. Degreasing helps to prevent these accidents by ensuring that equipment operates smoothly and efficiently. Regular maintenance and degreasing can identify potential issues before they escalate into safety hazards.
Read more about industrial parts cleaning here
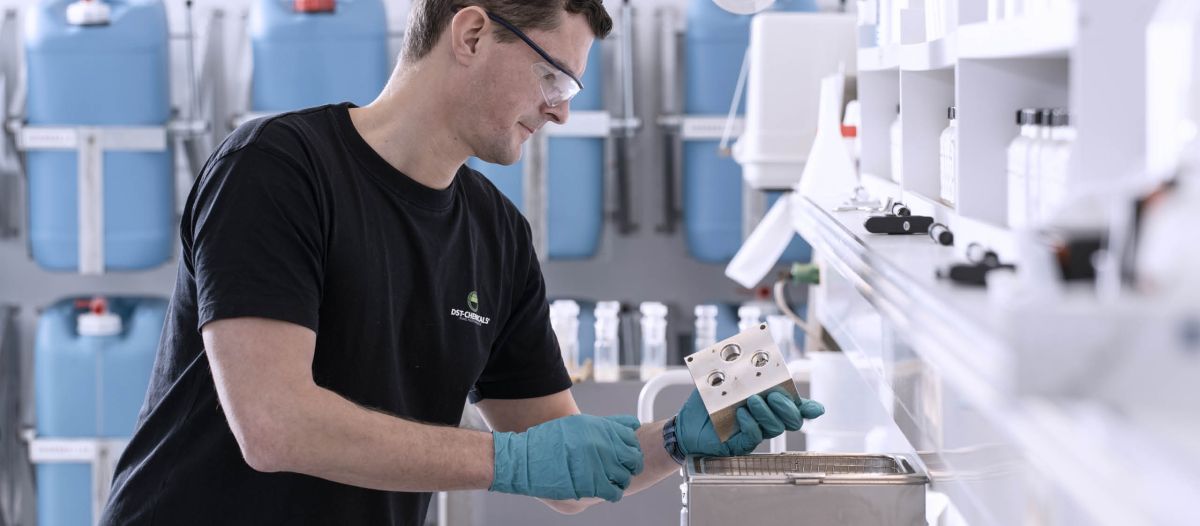
Best practices in industrial degreasing
Best practices in industrial degreasing are essential to ensure optimal performance, safety, and longevity of equipment. Here are some guidelines for maintaining degreasing equipment and implementing safety protocols:
1. Equipment Maintenance:
A) Instrument adjustment: Ensure that degreasing equipment is properly instrumented to ensure accurate and efficient cleaning.
B) Regular checks: Perform regular inspections of equipment for any signs of wear and tear, leaks, or malfunctions, and address any issues promptly.
C) Clean equipment: Thoroughly clean and maintain degreasing equipment to prevent contaminants from accumulating and affecting performance.
D) Follow manufacturer’s guidelines: Adhere to the manufacturer’s instructions for proper operation, maintenance, and storage of degreasing equipment.
2. Safety protocols:
A) Ventilation: Ensure adequate ventilation in the degreasing area to minimize exposure to fumes and vapors. Consider installing ventilation systems or using exhaust fans to remove airborne contaminants.
B) Protective gear: Provide appropriate personal protective equipment (PPE) such as gloves, goggles, and respirators to employees handling degreasers to protect against chemical exposure.
C) Training: Properly train employees in the safe handling and use of degreasers, including how to handle spills or accidents.
D) Disposal Procedures: Establish proper procedures for the disposal of degreasing chemicals and waste in compliance with regulations. Consider recycling or reusing degreasing solutions when possible.
3. Environmental considerations:
A) Use Eco-friendly degreasers: Consider using environmentally friendly degreasers that are biodegradable and safer for the environment.
B) spill prevention: Implement spill prevention measures and have appropriate spill response kits on hand in case of accidents.
C) Proper Storage: Store degreaser in a designated area away from heat sources, ignition points, and incompatible materials to prevent accidents.
How we can cover your needs with our industrial degreasers
You’ve learned a ton so far, and it’s totally normal if you’re feeling a bit overwhelmed and wondering how to choose the right industrial degreaser for your needs. Don’t worry, we’ve got your back if you need us!
Our degreasing solutions offer three key advantages that set them apart. Before diving into these benefits, it is crucial to highlight that all our DST-products are water-based, making them ideal for industrial environments. Firstly, our degreasers excel at operating at low temperatures, effectively cleaning and degreasing any metal surface.
Furthermore, they are foam-free from 38°C which means boosts cleaning efficiency. Secondly, the pH levels of our water-based DST-DEGREEZ products range from slightly acidic to neutral and slightly alkaline, facilitating safe degreasing of various metal types without compromising employee health. Lastly, our demulsifying DST-DEGREEZ products prolong bath life and minimize interruptions by separating oil from the washing solution, allowing for easy removal using an oil skimmer. Simplifying your workday, enhancing efficiency, and reducing downtime – all made possible with DST-DEGREEZ.
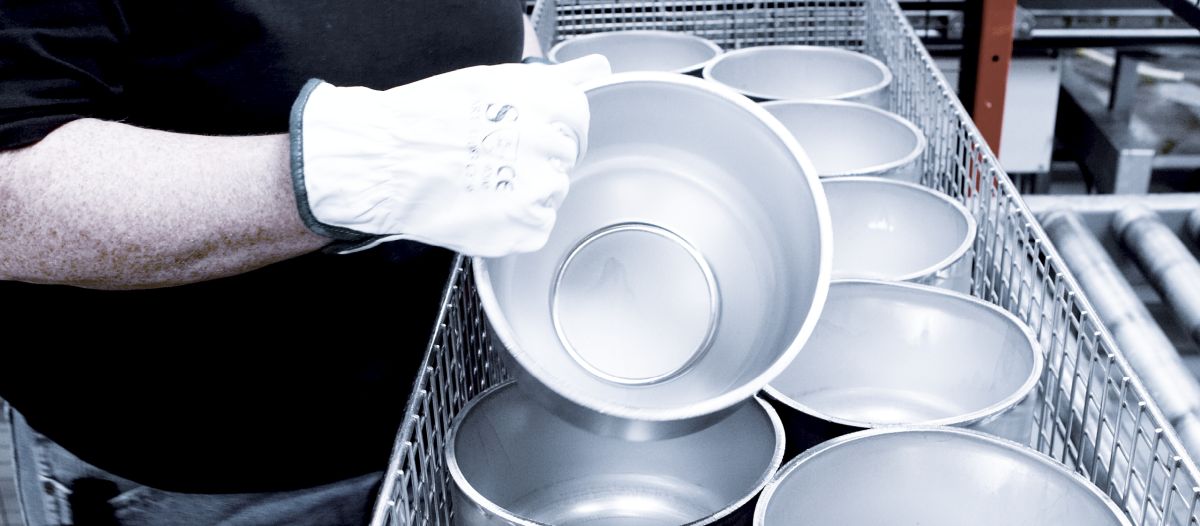
Questions & Answers
What is the industrial degreasing process? Industrial degreasing involves the removal of oils, greases, and contaminants from parts and equipment to maintain optimal performance and efficiency. This process typically involves the application of degreasing agent or solvents to dissolve or dislodge the contaminants, followed by rinsing or wiping to remove them from the surface.
What is an industrial degreaser? An industrial degreaser is a chemical agent or solvent specially designed to remove oils, grease, and contaminants from parts, equipment, machinery, and surfaces. Degreasers come in various formulations, including solvent-based, water-based, and environmentally friendly options, depending on the application and environmental considerations.
What are the environmental benefits of water-based degreasers? Water-based degreasers offer environmental benefits compared to solvent-based degreasers, as they are typically biodegradable and less harmful to the environment. They reduce the risk of air and water pollution, minimize chemical exposure to workers, and contribute to a more sustainable cleaning process.
How does degreasing prolong the lifespan of equipment? Degreasing helps to prolong the lifespan of equipment by reducing friction between moving parts, improving heat dissipation, and enhancing overall performance. With the removal of oil, grease, and other contaminants that can cause wear and tear on components, degreasing prevents premature equipment failure, extends maintenance intervals, and ensures optimal functionality and efficiency.
Nick Bjerregaard
International Process & Technical Manager
Technical Manager at DST-CHEMICALS: 20 years of chemical industry experience, driving innovation, efficiency, and environmental sustainability.
Environmental, social and governance
At DST-CHEMICALS, sustainability is at the heart of everything we do. We engaged with key stakeholders, including our team of suppliers, to ensure we focused on what truly mattered. Ready to see the full picture? Keep an eye out for our ESG report, where we share the next steps in our journey to sustainability.