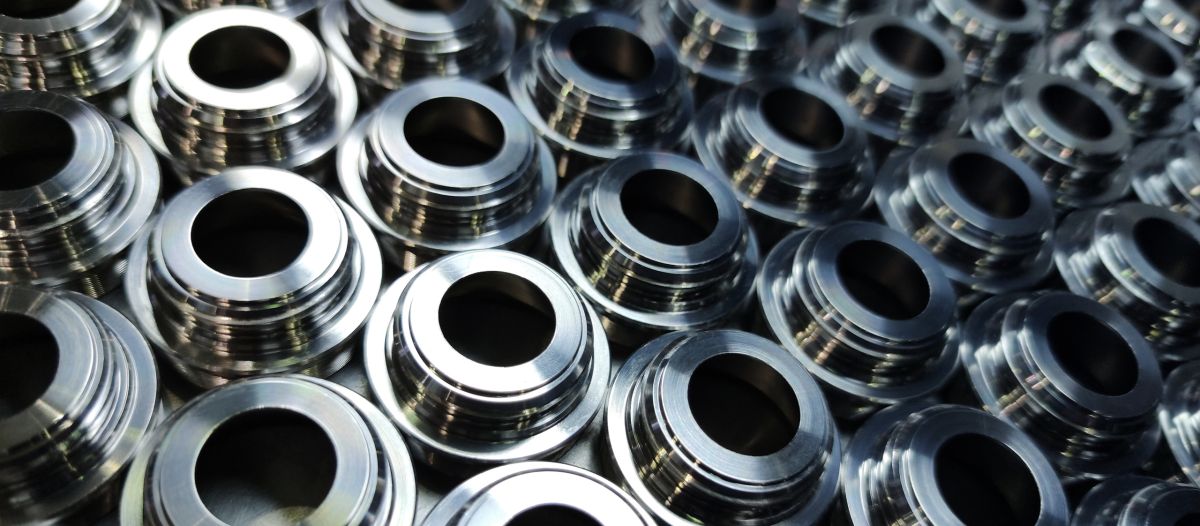
When it comes to high-precision manufacturing, removing burrs is only half the battle. Thermal deburring (TEM) is a powerful method for eliminating unwanted edges in complex parts—but it also leaves behind challenging residues that can compromise both quality and performance if not handled correctly.
In this blog post, we will explore why post-deburring cleaning is essential, the types of contaminants to watch out for, and how the right cleaning methods and chemistry can make all the difference. Whether you’re in automotive, manufacturing, or off-road-vehicles (ORVs), a clean finish is not optional, it’s critical.
Table of Contents
Why cleaning after thermal deburring matters
Thermal deburring (TEM) is a highly effective method used in the manufacturing industry to eliminate burrs from hard-to-reach areas of complex metal parts. This process uses a burst of heat and gas in a sealed chamber to vaporise burrs instantly. However, while efficient, it also leaves behind undesirable residues such as carbonised particles, oxidation layers, and metallic dust.
If not properly cleaned, these residues can:
Compromise the dimensional accuracy of precision parts.
Interfere with coating or plating processes.
Cause issues in assembly or functionality of components.
Lead to premature wear or failure in sensitive applications
Proper post-deburring cleaning is essential to restore the component to its intended cleanliness, surface finish, and performance standards. By using the right cleaning chemistry and method tailored to thermal deburring residues, manufacturers can ensure high product quality and process reliability.
Read more about DST-DEBURR here
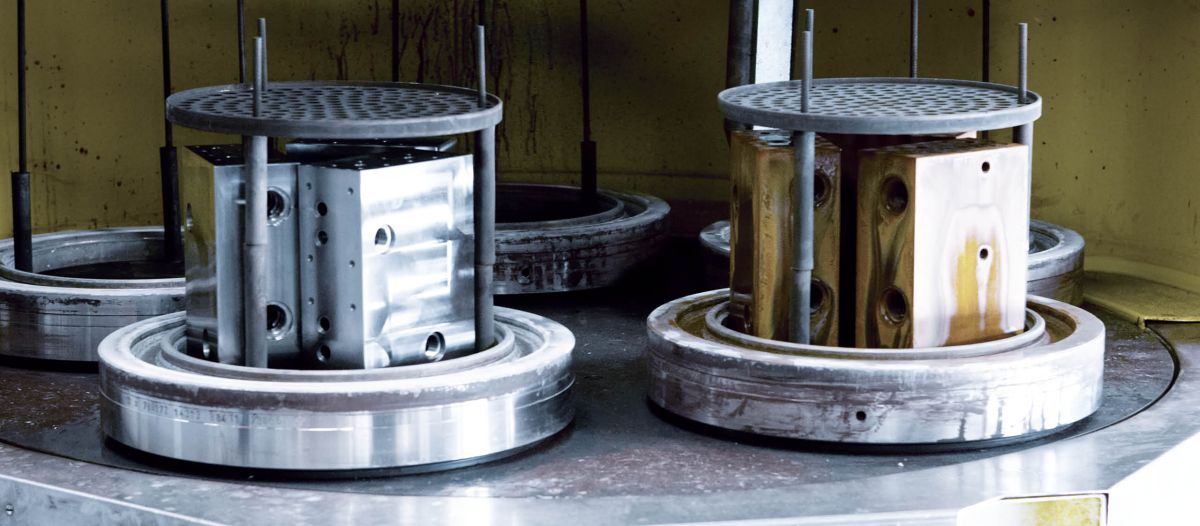
Key goals of post-deburring cleaning
Post-deburring cleaning plays a critical role in maintaining the quality and performance of precision components. After thermal deburring, it’s not just about making the part look clean — it’s about preparing it for the next stage of production or end use.
The main goals of effective post-TEM cleaning include:
Preserving dimensional and surface integrity
Residues like oxidation or metallic dust can alter surface measurements, especially in precision-engineered parts. Cleaning ensures exact tolerances are maintained.
Ensuring proper functionality and fit
Any leftover debris can interfere with the mechanical operation of moving parts or cause misalignments during assembly.
Guaranteeing long-term reliability
Contaminants can lead to corrosion, fatigue, or premature failure, especially in demanding environments like manufacturing.
Meeting industry and regulatory standards
Many industries have strict cleanliness and quality requirements (e.g., ISO, GHS, CLP, REACH) that demand a clean, contaminant-free surface before further processing or product delivery.
Effective post-deburring cleaning ensures that each component not only performs as intended but also meets customer expectations and industry benchmarks.
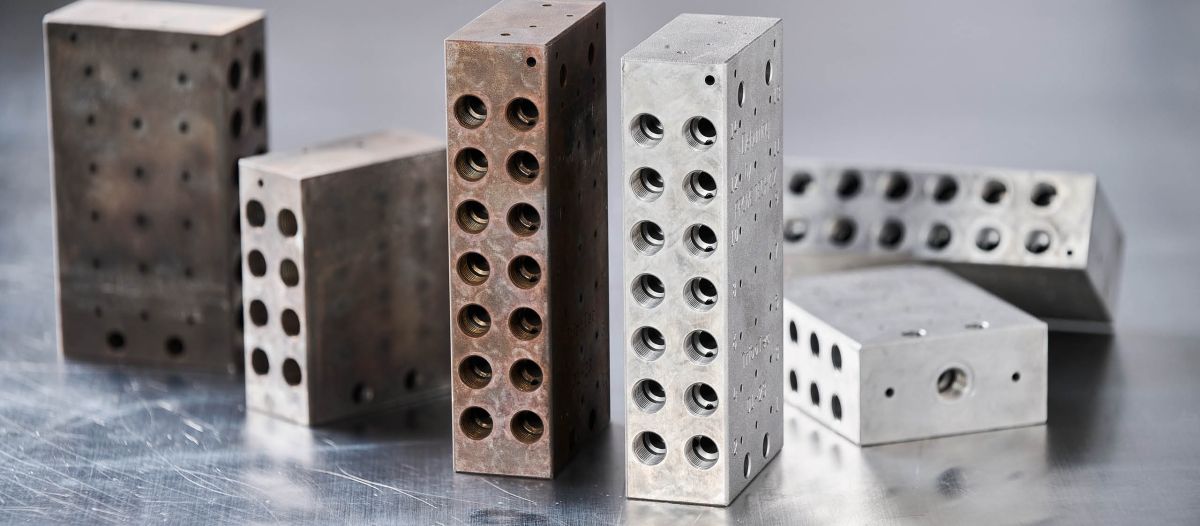
Recommended cleaning methods
After thermal deburring, selecting the right cleaning method is essential to remove all residual contaminants and prepare the component for its next stage. While several techniques are available, ultrasonic cleaning and water-based solutions stand out for their efficiency, safety, and eco-consciousness.
Ultrasonic cleaning
Ultrasonic cleaning is highly effective at reaching into blind holes, narrow passages, and complex geometries, exactly where burrs and residues tend to hide. High-frequency sound waves create microscopic bubbles in a cleaning solution, which implode and dislodge particles like carbonised dust, oxidation, and metallic debris without damaging the part.
Key benefits:
Reaches hard-to-clean areas
Gentle on delicate or precision parts If not over exposed
Compatible with water-based detergents
Fast and repeatable process
Water-based cleaning
Water-based cleaning solutions offer a sustainable and powerful alternative to solvent-based options. These systems can be tailored with detergents designed to break down specific contaminants left after thermal deburring, such as oxidation layers and carbon residues.
Key benefits:
Environmentally responsible (less toxic, less VOC)
Cost-effective for large-scale or continuous operations
Easy to integrate with automated cleaning plants
Safe for workers and compliant with environmental regulations
Solvent-based cleaning (use with caution)
While solvent-based cleaning has historically been used in industrial cleaning, they come with increasing regulatory restrictions and safety concerns. Solvents can be effective but may pose health, environmental, and disposal challenges, making them less desirable for forward-thinking manufacturers.
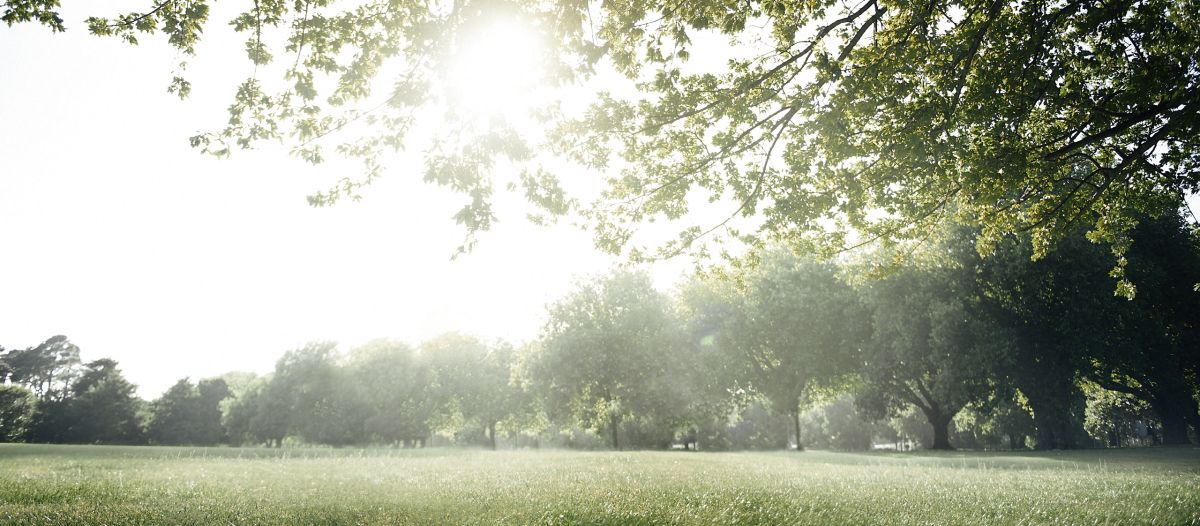
See how we have helped others
We’ve done it before. Actually, we have helped professionals like you bring new life to machines since 1987. Roland Fleischer GmbH is a prime example of this.
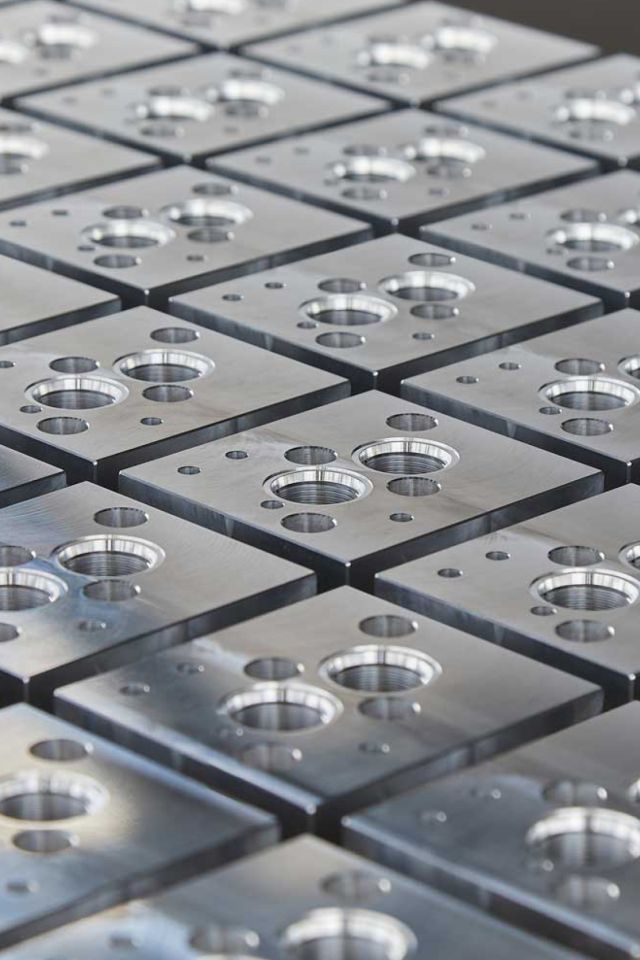
Roland Fleischer
Optimising contract deburring
Roland Fleischer GmbH is a German company specialising in CNC machining and contract deburring for hydraulic blocks and plates. They provide high-quality, efficient deburring services, reducing the need for manual rework and improving the quality of finished products.
Choosing the right cleaning chemistry
Selecting the right cleaning chemistry is just as important as choosing the cleaning method itself. We specialize in water-based, eco-conscious cleaning solutions designed to effectively remove contaminants left after thermal deburring — without compromising on sustainability or performance. What sets us apart is our result-oriented approach: we don’t just offer products, we deliver solutions tailored to your specific needs.
Lab-tested solutions with a product selector report
Before recommending a solution, we will test the type of contamination from your facility that we have acquired as a sample in our in-house laboratory. Through our Product Selector Report, we identify the most effective cleaning product for your exact need, contaminant type, and production process — ensuring you get the best possible results from day one.
Dedicated Technical Advisor — at no extra cost
From the first conversation to full implementation and beyond, you’ll be assigned a dedicated technical advisor. This specialist supports you before, during, and after conversion — helping optimize your process, fine-tune chemistry, and troubleshoot any challenges. And the best part? This personalized support is completely cost-free.
Questions and answers
Why is cleaning necessary after thermal deburring?
Thermal deburring leaves behind contaminants such as carbonized particles, oxidation layers, and metallic dust. Without proper cleaning, these residues can compromise part precision, assembly, and long-term reliability — especially in high-performance applications.
What are the most effective cleaning methods after thermal deburring?
Ultrasonic cleaning and water-based cleaning systems are the most effective and sustainable methods. They remove stubborn residues safely and are suitable for complex geometries without damaging the part.
Are water-based cleaners strong enough to remove post-deburring residues?
Absolutely. Modern water-based cleaning solutions — like those developed by us— are specifically formulated to break down oxidation, carbon buildup, and metal particles while being safer for both workers and the environment.
How do we ensure the right cleaning product is chosen?
We test your actual components in our in-house tech lab and provide a tailored Product Selector Report. This ensures we recommend the most effective and cost-efficient solution based on real data, not assumptions.
Will I get support during the transition to a new cleaning solution?
Yes. Every customer is assigned a dedicated technical advisor who supports you before, during, and after conversion — and this service is completely cost-free.
Nick Bjerregaard
International Process & Technical Manager
Technical Manager at DST-CHEMICALS: 20 years of chemical industry experience, driving innovation, efficiency, and environmental sustainability.
Environmental, social and governance
Environmental, social and governance At DST-CHEMICALS, sustainability is at the heart of everything we do. We engaged with key stakeholders, including our team of suppliers, to ensure we focused on what truly mattered. Ready to see the full picture? Take a look at our ESG report, where we share the next steps in our journey to sustainability.