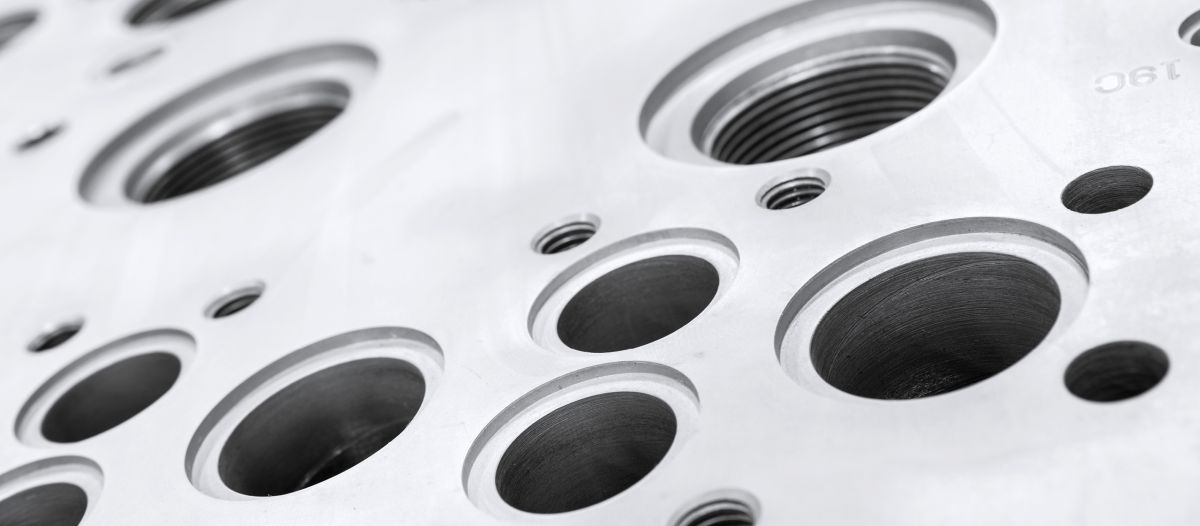
Metal deburring refers to the process of removing burrs or sharp edges from metal surfaces. It is a crucial step in metalworking as it improves the overall quality, safety, and functionality of the metal parts. DST-CHEMICALS specializes in providing cleaning solutions after the metal deburring process.
Table of Contents
What is metal deburring?
Metal deburring is the process of removing burrs or rough edges from metal surfaces. Burrs are small, unwanted protrusions that can occur during the manufacturing or machining of metal parts. Removing these burrs is important as it improves the overall quality of the metal part, ensuring smooth surfaces and precise dimensions. Deburring also plays a crucial role in enhancing the functionality and safety of metal parts, as it eliminates sharp edges that could cause injury or damage during handling or assembly.
Deburring techniques for different metals
Metal-specific deburring techniques vary depending on the type of metal being worked with. Steel is a common metal for deburring due to its widespread use in various industries. Techniques for steel deburring include manual methods such as filing, sanding, or using abrasive wheels. Additionally, automated methods like tumbling, vibratory finishing, or using specialized deburring machines can be employed.
When deburring other metals like aluminum or brass, it is important to consider their unique characteristics. Aluminum, for example, is a softer metal and can be more prone to galling or smearing during the deburring process. Brass, on the other hand, is a softer metal that can be easily scratched or damaged. Care must be taken to select deburring methods that are gentle and minimize the risk of surface damage.
Therefore, techniques such as using thermal or electrochemical deburring methods may be more suitable. Thermal deburring, also known as thermal energy method or TEM, involves using a combination of heat and pressure to remove burrs from steel parts. The process utilizes a high-temperature gas mixture that is directed at the burrs, causing them to thermally soften and be easily removed. This method is particularly effective for complex or hard-to-reach areas.
Electrochemical deburring, on the other hand, utilizes the principle of electrolysis to remove burrs from steel surfaces. It involves immersing the steel part in an electrolyte solution and applying a low-voltage electrical current. The current causes the burrs to dissolve or be selectively removed, leaving behind a smooth surface. This method is often used for precision deburring of intricate or delicate steel parts.
In summary, different metals require specific deburring techniques to achieve optimal results. Understanding the properties and characteristics of each metal is crucial in selecting the appropriate deburring method to ensure high-quality, burr-free surfaces.
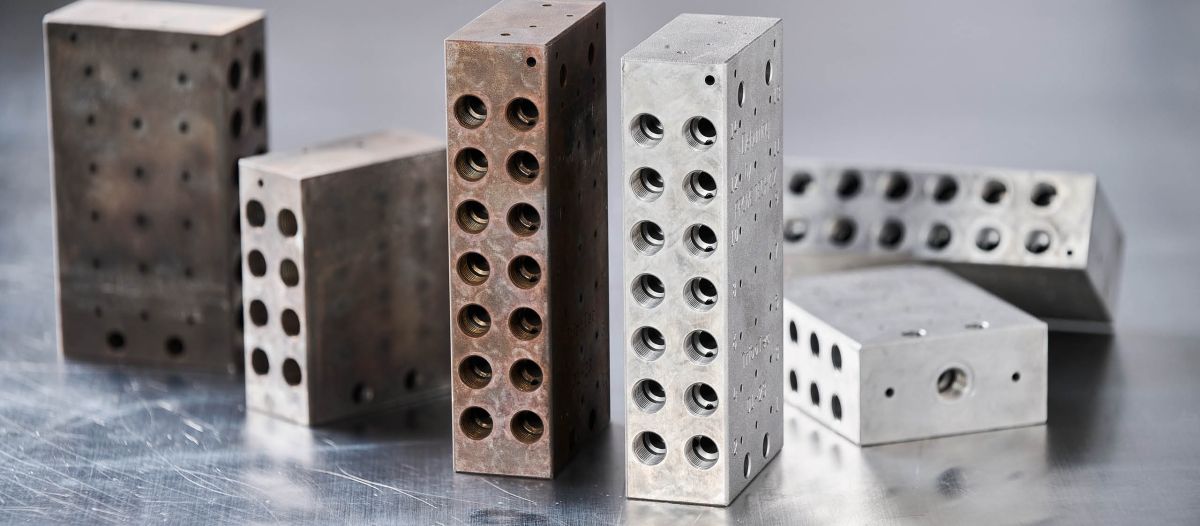
Deburring tools for metal
Deburring tools designed for metal are essential for achieving effective and efficient deburring results. There are various types of deburring tools suitable for metal deburring, including manual tools, mechanical tools, TEM (Thermal) tools, and ECM (Electrochemical) tools.
Manual deburring tools, such as files and scrapers, are commonly used for smaller or intricate metal parts. They allow for precise control and can be used to remove burrs by hand.
Mechanical deburring tools, such as deburring machines or rotary deburring tools, are suitable for larger or more complex metal parts. These tools use rotating abrasive wheels or brushes to remove burrs quickly and consistently.
TEM tools utilize thermal energy, such as hot air or flames, to remove burrs from metal surfaces. This method is often used for heat-resistant metals or parts with specific surface requirements.
ECM tools employ electrochemical reactions to selectively dissolve burrs from metal surfaces. This technique is particularly effective for complex shapes or delicate parts.
When selecting the appropriate deburring tool for metal, several factors should be considered. These include the type and size of the metal part, the severity of the burrs, the desired surface finish, and the production volume. It is important to choose a tool that matches the specific requirements of the metal and the deburring task at hand to achieve optimal results.
By considering the available options and evaluating the specific needs of the metal deburring process, one can select the most suitable deburring tool for efficient and high-quality results.
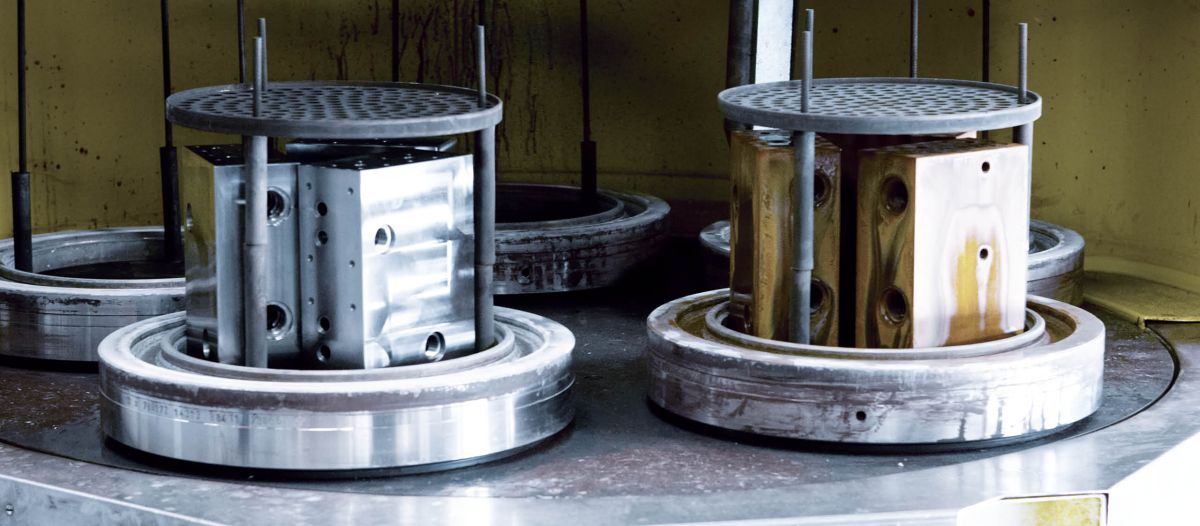
See how we have helped others
We’ve done it before. Actually, we have helped professionals like you bring new life to machines since 1987. Roland Fleischer GmbH is a prime example of this.
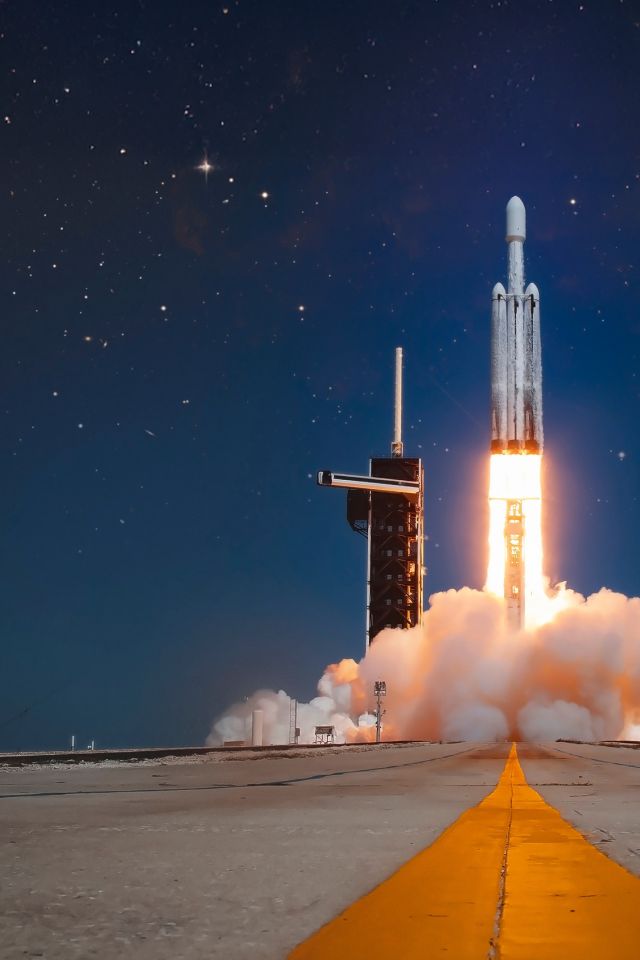
Roland Fleischer
Optimising contract deburring
Roland Fleischer GmbH is a German company specialising in CNC machining and contract deburring for hydraulic blocks and plates. They provide high-quality, efficient deburring services, reducing the need for manual rework and improving the quality of finished products.
Conclusion
What is deburring metal?
Metal deburring is the process of removing sharp edges, raised edges, or rough spots called burrs from metal surfaces.
What do you use to deburr metal?
To deburr metal, various tools and methods can be used, such as grinding wheels. Files, brushes, sandpaper, or specialized deburring machines for electrochemical or thermal energy processes.
What does burrs mean metal?
Burrs in metal refer to the unwanted imperfections or irregularities that can occur during metalworking, like sharp edges or small pieces of material sticking out.
What is the use of deburring?
The main purpose of deburring is to improve the safety, quality, and functionality of metal components. It helps to avoid injury from sharp edges, enhances precision in assembly or machining processes, and improves the overall appearance of the metal part.
Nick Bjerregaard
International Process & Technical Manager
Technical Manager at DST-CHEMICALS: 20 years of chemical industry experience, driving innovation, efficiency, and environmental sustainability.
Environmental, social and governance
At DST-CHEMICALS, sustainability is at the heart of everything we do. We engaged with key stakeholders, including our team of suppliers, to ensure we focused on what truly mattered. Ready to see the full picture? Keep an eye out for our ESG report, where we share the next steps in our journey to sustainability.