Deburring, a process of removing sharp edges and burrs from metal surfaces from metal surfaces, plays a crucial role in the manufacturing industry. Among the various materials that require deburring, aluminum is one that demands special attention due to its unique characteristics. Dive deeper into the world of aluminum deburring, exploring its significance in manufacturing and gain insight on how we can help you clean after your deburring process.
Table of Contents
Why Deburr Aluminum?
To begin with, let’s define what aluminum deburring is. When aluminum components are produced through casting, milling, or other machining processes, sharp edges, burrs, and rough surfaces are often left behind. These imperfections not only compromised the aesthetics of the product but can also lead to functionality issues and safety hazards if not addressed. Aluminum deburring involves the removal of these undesired imperfections, resulting in smooth, polished, and safe surfaces.
The significance of aluminum deburring in the manufacturing industry cannot be emphasized enough. Firstly, it ensures the quality of the final product. By eliminating burrs and sharp edges, manufacturers can prevent potential injury to end-users and enhance the functionality of their products. Secondly, aluminum deburring improves the overall appearance of the components. Smooth and polished surfaces not only give a professional and refined look but also contribute to the longevity of the product.
If you are deburring you are also looking to clean after the process. Let’s introduce our selection of high-quality solutions for cleaning after aluminum deburring, encompassing exquisite products designed to impeccably clean and degrease the deburred parts. With an extensive expertise spanning over 35 years in this field, we recognize the unique nature of each cleaning endeavor, necessitating a unique approach. We call this the Pure Performance Concept. Thus, in the realm of modern deburring techniques, the pursuit of excellence extends to modernized cleaning solutions.
Electrochemical deburring (ECM) is commonly used to remove burrs from metal workpieces. In this process, an electrolyte solution containing salt or glycol is employed to utilize electrochemical energy for deburring. By functioning as a cathode and applying a direct current (DC) along with the electrolyte fluid, the deburring equipment triggers an anodic reaction. This method efficiently and precisely eliminates burrs without causing any harm to the surrounding metal.
Read more about deburring methods here
To achieve precision in aluminum deburring, certain tips should be kept in mind. First and foremost, understanding the specific characteristics and properties of the aluminum component is essential. This knowledge helps in selecting the appropriate deburring technique and tools. Additionally, closely monitoring the deburring process and periodically inspecting the quality of the deburred surfaces is crucial to ensure desired results.
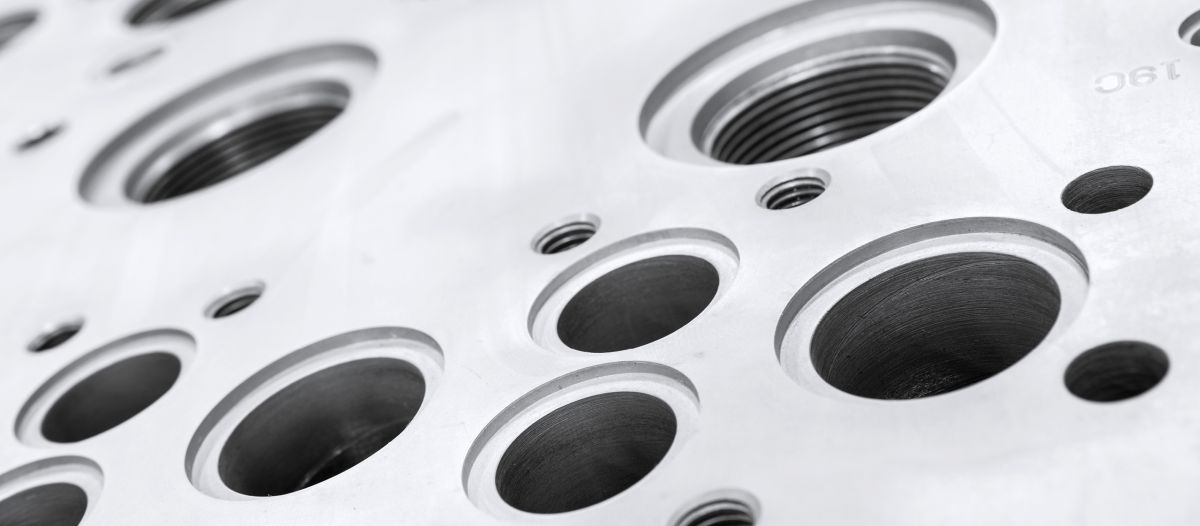
Deburring Techniques for Aluminum
Aluminum, known for its lightweight and corrosion-resistant properties, is a popular choice across industries like automotive, aerospace, and construction. However, due to its malleability, susceptibility to burrs and sharp edges is inevitable during the manufacturing process. Removing these burrs not only improves the aesthetics of the final product but also ensures safety by eliminating potential hazards. Some of the deburring methods includes. manual, mechanical, thermal, and electrochemical deburring.
Read about DEBURRING methods here
Deburring Aluminum Extrusions: Challenges and Solutions. Aluminum extrusions present specific challenges during the deburring process. Due to their elongated shapes and various profiles, optimizing deburring techniques becomes crucial. One common challenge in deburring aluminum extrusions is the removal of burrs from internal cavities or intricate profiles. Manual or mechanical deburring may not effectively address these hard-to-reach areas. In such cases, thermal or electrochemical deburring techniques prove highly advantageous, ensuring a thorough removal of burrs from challenging locations. Another challenge lies in maintaining the integrity of the extruded profiles and avoiding damage during the deburring process. Specialized fixtures or jigs are often utilized to secure the extrusions and ensure precise deburring without altering the desired shape.
Professional Guidance for cleaning after aluminum deburring
Over the years we have established ourselves as a leading provider of innovative and efficient cleaning solutions after aluminum deburring. With a proven track record of delivering exceptional results, we have earned a reputation as the go-to cleaning company for industries seeking top-notch cleaning after a deburring process.
Our strong expertise in cleaning after aluminum deburring rests on the foundation of our “Pure Performance” concept. This concept encompasses several key features that set us apart from competitors.
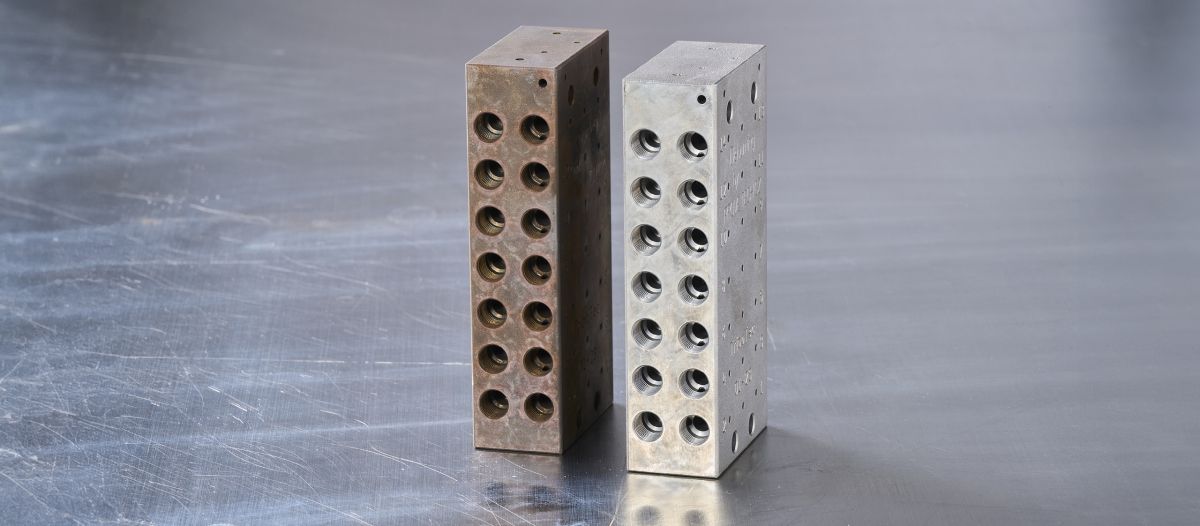
See how we have helped others
We’ve done it before. Actually, we have helped professionals like you bring new life to machines since 1987. Roland Fleischer GmbH is a prime example of this.
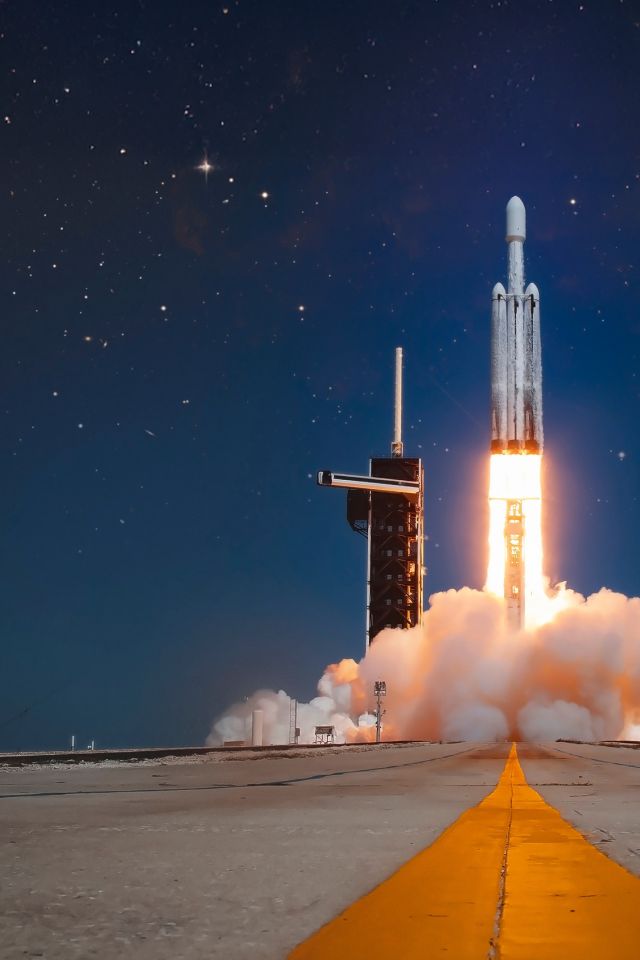
Roland Fleischer
Optimising contract deburring
Roland Fleischer GmbH is a German company specialising in CNC machining and contract deburring for hydraulic blocks and plates. They provide high-quality, efficient deburring services, reducing the need for manual rework and improving the quality of finished products.
Pro Tips for Achieving Quality Aluminum Deburring
At DST-CHEMICALS, we are a leading supplier of surface treating cleaning products and have over 35 years of experience within the field. Therefore, we would like to share some valueable insights into achieving effective aluminum deburring. First and foremost, maintaining your deburring tools in optimum condition is crucial for achieving effective aluminum deburring. Regularly inspect and clean your tools to prevent buildup of debris and ensure that the working area is clear. Choose the appropriate tools based on the size and type of burrs and be sure to use sharp blades to minimize the risk of creating additional marks or scratches on the aluminum surface. Replace worn-out tools promptly to avoid compromises in the deburring process.
Second, consistency is key to achieving uniform and high-quality deburring results. Establishing a standard procedure for deburring aluminum parts helps ensure that each piece receives the same level of attention and treatment. Train your deburring operators to follow specific techniques, such as using the right amount of pressure, maintaining a continuous motion, and ensuring that the tool reaches all areas requiring deburring. Consistent techniques eliminate inconsistencies in the finished product, enhancing overall quality.
Even with the best tools and techniques, aluminum deburring can present challenges that require troubleshooting. Some common issues include:
Recurring Burrs: If you find that burrs keep reappearing after deburring, it might be due to improper tool alignment or insufficient pressure. Ensure that the tool is correctly aligned with the burr and apply sufficient pressure to remove the excess material.
Heat Generation and surface discoloration: Deburring can generate excessive heat, causing unwanted surface discoloration and compromising the aluminum’s integrity. Make sure to use coolant or lubricants during the deburring process to manage heat generation effectively.
Questions & Answers
What is the best way to deburr aluminum?
The best way to deburr aluminum can depend on the specific requirements and resources available. The traditional method includes using a tool like blade, sandpaper, or a grinding wheel. Alternatively, thermal deburring (TEM) and electrochemical deburring (ECM) are usually more effective methods.
What is deburring aluminum?
Deburring aluminum refers to the process of removing sharp edges, rough spots, or burrs from aluminum surfaces after they have been machined or cut. TEM employs a combination of pressure and explosive gases to quickly remove burrs by utilizing the heat generated in the process. ECM uses a combination of electrolyte and electrical current to dissolve burrs selectively.
How do you use an aluminum deburring tool?
To use an aluminum deburring tool, hold the tool firmly and apply gentle pressure to the burr or rough spots. Move the tool back and forth or in circular motions until the desired smoothness is achieved. Similarly, TEM and ECM can be carried out using specific equipment and following the recommended procedures provided by the manufacturers.
How do you remove aluminum burrs?
To remove aluminum burrs, various methods can be used. Traditionally, a blade or a file can be used as mentioned earlier. Additionally, TEM can effectively remove burrs in hard-to-reach areas and complex shapes, while ECM is suitable for precise and intricate parts.
Nick Bjerregaard
International Process & Technical Manager
Technical Manager at DST-CHEMICALS: 20 years of chemical industry experience, driving innovation, efficiency, and environmental sustainability.
Environmental, social and governance
At DST-CHEMICALS, sustainability is at the heart of everything we do. We engaged with key stakeholders, including our team of suppliers, to ensure we focused on what truly mattered. Ready to see the full picture? Keep an eye out for our ESG report, where we share the next steps in our journey to sustainability.