
Corrosion is a common problem that can wreak havoc on metal surfaces, causing them to deteriorate and lose their structural integrity over time. In order to prevent corrosion and extend metal surfaces, it is essential to choose the best coatings to protect against corrosion. In this blog post, we will discuss how to choose the best coatings to protect against corrosion.
Table of Contents
Different types of coatings for corrosion protection
There are various types of coatings available for corrosion protection, each with its own unique properties and benefits. The reason for the diversity in coatings is that different types of metals and environments require different levels of protection. Factors such as the metal surface, the environmental conditions it will be exposed to, and the desired longevity of the coating all play a role in determining the most suitable type of coating.
Read about aluminium corrosion protection here
List of different types of coatings:
1. Epoxy coatings
2. Alkyd coatings
3. Silicone coatings
4. Acrylic coatings
5. DST-PAS
Each of these coatings offers unique benefits and protection against corrosion, making it essential to choose the right one based on the specific requirements of the metal surface and environmental conditions. By selecting the appropriate coating, you can effectively protect metal surfaces from corrosion and extend their lifespan.
Epoxy coatings
Epoxy coatings are known for their exceptional durability and chemical resistance, making them a popular choice for corrosion protection. These coatings are typically used on metal surfaces in industrial settings where they are exposed to harsh chemicals, high temperature, and heavy wear and tear. Epoxy coatings form a strong bond with a metal surface, creating a protective barrier that prevents corrosion from occurring.
Surface compatibility: Epoxy coatings are suitable for a wide range of metal surfaces, including steel, aluminium, iron etc. They ae commonly used on surfaces that are exposed to corrosive chemicals, water, and extreme temperatures.
Environments: Epoxy coatings are most used in industrial environments where metal surfaces are exposed to harsh conditions, such as chemical processing plants, oil refineries, and wastewater treatment facilities. These coatings are also used in commercial and residential settings for flooring, countertops, and other applications where corrosion protection is required.
Pros of epoxy coatings:
- Strong adherence to metal surfaces.
- Excellent durability and chemical resistance.
- High resistance to abrasion and impact.
- Easy to clean and maintain.
- Provides a smooth, glossy finish.
Cons of epoxy coatings:
- May degrade when exposed to UV radiation.
- Can be prone to yellowing or discoloration over time.
- Requires proper surface preparation for optimal adhesion.
- Can be more costly than other coating options.
Alkyd coatings
Alkyd coatings are known for their versatility and durability, making them a popular choice for corrosion protection on a variety of surfaces. These coatings are oil-based and provide a protective barrier against moisture, chemicals, and environmental factors that can cause corrosion. Alkyd coatings are known for their excellent adhesion properties, making them suitable for a wide range of metal surfaces.
Surface compatibility: Alkyd coatings are suitable for a variety of metal surfaces, including steel, iron, and aluminium. They are commonly used on surfaces that are surfaces that are exposed to mild to moderate levels of corrosion, such as equipment, machinery, and structural components in industrial and commercial settings.
Environments: Alkyd coatings are most used in indoor and outdoor environments where metal surfaces are subject to moderate levels of corrosion. They are frequently used in applications such as machinery, structural steel, manufacturing facilities etc.
Pros of alkyd coatings:
- Good adhesion to metal surfaces.
- Versatile and suitable for a variety of substrates.
- Excellent resistance to moisture and chemicals.
- Dries quickly and provides a smooth finish.
- Easy to apply and maintain.
Cons of alkyd coatings:
- Limited resistance to high temperatures.
- Susceptible to cracking and peeling over time.
- Not as durable as some other coating options.
- May require multiple coats for adequate protection.
Silicone coatings
Silicone coatings are known for their excellent weather resistance, UV stability, and high temperature resistance, making them a popular choice for corrosion protection in harsh environments. These coatings form a flexible and durable barrier on metal surfaces, providing long-lasting protection against corrosion, moisture, chemicals, and extreme temperatures. Silicone coatings are commonly used in applications where high-performance protection is required.
Surface Compatibility: Silicone coatings are suitable for a variety of surfaces, including metal surfaces exposed to extreme environmental conditions, such as roofs, bridges, pipelines, and equipment in industrial settings.
Environments: Silicone coatings are most used in outdoor environments where metal surfaces are subject to harsh weather conditions, UV exposure, and high temperatures. They are frequently used in applications such as industrial roofs, bridges, marine structures, and equipment in chemical processing plants and refineries.
Pros of silicone coatings:
- Excellent weather resistance and UV stability.
- High temperature resistance.
- Flexible and durable coating that can accommodate movement.
- Low maintenance and long service life.
- Provides a smooth and aesthetics finish.
Cons of silicone coatings:
- Higher cost compared to other coating options.
- Limited abrasion and impact resistance.
- Requires proper surface preparation for optimal adhesion.
- May degrade over time in environments with high chemical exposure.
Acrylic coatings
Acrylic coatings are known for their versatility, durability, and ease of application, making them a popular choice for corrosion protection on a variety of surface. These coatings are water-based and provide a protective barrier against moisture, chemicals, and environmental factors that can cause corrosion. Acrylic coatings are known for their excellent adhesion properties and resistance to UV exposure, making them suitable for both interior and exterior applications.
Surface compatibility: Acrylic coatings are suitable for a variety of surfaces, including metal, word, concrete, and masonry. They are commonly used on metal surfaces exposed to mild to moderate levels of corrosion, such as structural components, equipment, and machinery in commercial and residential settings.
Environments: Acrylic coatings are most used in indoor and outdoor environments where metal surfaces are subject to moderate levels of corrosion. They are frequently used in applications such as architectural structures, machinery, furniture’s, and decorative metalwork in residential, commercial, and institutional buildings.
Pros of acrylic coatings:
- Good adhesion to a variety of surfaces.
- Excellent UV resistance and colour retention.
- Fast drying time and easy application.
- Low odour.
- Provide a smooth and attractive finish.
Cons of acrylic coatings:
- Limited resistance to harsh chemicals and abrasion.
- Not as durable as some other coating options.
- May require multiple coats for adequate protection.
- Vulnerable to hot temperatures and high humidity environments.
DST-PAS
The DST-PAS is one of our many exceptional products with focus on functionality for both long- and short-term protection. Whether transporting goods overseas, the DST-PAS effectively shields against humidity and complies with all finishing passivation standards, even functioning optimally at 20°C. Furthermore, our water-based DST-PAS products boast a pH range from neutral to slightly alkaline, meticulously formulated to cater to all metal types while prioritizing a safe working environment. Imagine the convenience of painting directly on parts without the need for additional washing – a reality achievable with DST-PAS. Simplifying indoor storage with its temporary corrosion inhibitor, DST-PAS truly enhances efficiency and ease in your operations.
Pros of DST-PAS:
- Suitable for all metal types.
- Water-based and enviro-friendly.
- Fast and easy application.
- Functions even at low temperatures.
- Enhances efficiency in operations.
Cons of DST-PAS:
- Requires specialized application procedures and training.
- Temporary corrosion inhibitor.
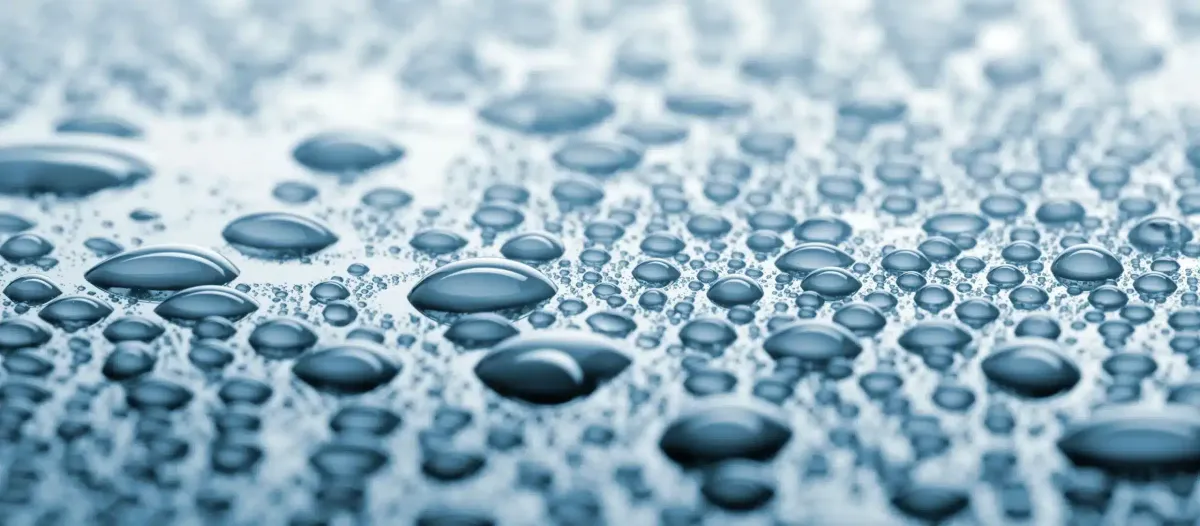
What application techniques are needed for corrosion protection coatings?
Application techniques for corrosion protection coatings vary depending on the type of coating, the surface being coated, and the specific environmental conditions. However, some common application techniques used for corrosion protection coatings include:
1. Surface preparation: Before applying any corrosion protection coating, the surface must be properly prepared to ensure adhesion and effectiveness. Surface preparation techniques may include cleaning, degreasing, chemical treatment to remove contaminants, rust, and old coatings.
Read more about DST-DEGREEZ
2. Spray Application: Spray application is one of the most common methods for applying corrosion protection coatings. This technique involves using a spray gun to atomise the coating material and evenly distribute it onto the surface. Spray application allows for a uniform and consistent coating thickness and is suitable for large surface areas.
3. Dip coating: Dip coating involves immersing the object or component into a tank of coating material to apply a uniform layer of protection. This method is commonly used for small, complex-shaped parts or components that are difficult to coat using other techniques.
Environmental considerations about corrosion protection coatings
Environmental considerations are increasingly important in the selection and application of corrosion protection coatings. As the awareness of environmental sustainability and the impact of the traditional coatings on the environment grows, there is a growing demand for eco-conscious coatings solutions. Here are some key points to consider regarding environmental aspects of corrosion protection coatings:
1. Eco-conscious coatings: Many manufacturers have developed eco-friendly coatings that have lower volatile organic compound (VOC) emissions, reduced toxicity, and are formulated using renewable or recyclable material. Examples of eco-friendly coatings include water-based coatings, powder coatings, and high-solids coatings that have lower environmental impact compared to traditional solvent-based coatings.
2. Low volatile organic compounds (VOC): are chemicals that evaporate into the air, contributing to air pollution and potential working safety. Low VOC coatings are formulated to have minimal VOC emissions, reducing air pollution and creating a healthier working environment during application.
3. Water-based coatings: Water-based coatings use water as a carrier instead of solvents, reducing emissions of harmful chemicals into the environment. Water-based coatings are environmentally friendly, safe to use, and provide effective corrosion protection for various surfaces.
Read more about our water-based products
Conclusion
In conclusion, when applying corrosion protection coatings, it is crucial to consider the environmental impact of the coatings and the application techniques used. Choosing eco-friendly coatings, such as water-based coatings, can help to reduce VOC emissions and minimize harmful effects on the environment. Proper surface preparation, application techniques, and disposal practices are essential for achieving effective and long-lasting corrosion protection while maintaining environmental sustainability. By selecting eco-friendly coating and implementing eco-friendly practices, we can protect against corrosion while minimizing our impact on the environment.
Nick Bjerregaard
International Process & Technical Manager
Technical Manager at DST-CHEMICALS: 20 years of chemical industry experience, driving innovation, efficiency, and environmental sustainability.
Environmental, social and governance
At DST-CHEMICALS, sustainability is at the heart of everything we do. We engaged with key stakeholders, including our team of suppliers, to ensure we focused on what truly mattered. Ready to see the full picture? Keep an eye out for our ESG report, where we share the next steps in our journey to sustainability.